Office building partition walls made from old window glass – carbon footprint cut in half
During the renovation of office building in Kaikukatu 3, Helsinki, a unique pilot explored how intact window elements could be reused in an office building’s interior spaces. The result was durable, movable glass partition walls with a carbon footprint just half that of new equivalents.
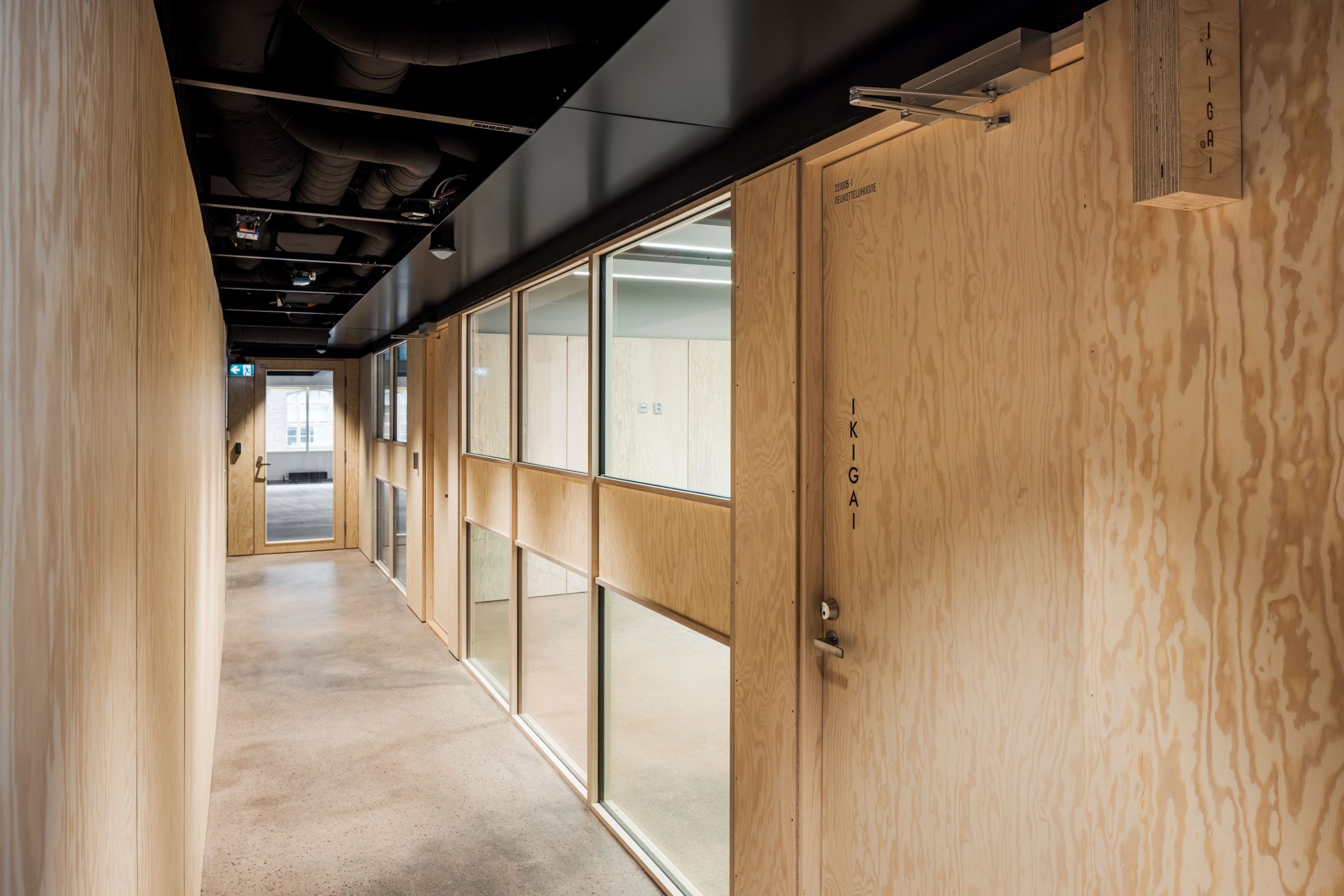
This text was translated with the help of AI.
Building renovations generate a massive amount of demolition material, much of which typically ends up as waste. In the renovation of an office building in Helsinki’s Sörnäinen district, the goal was to minimize demolition and make use of existing structures whenever environmentally and economically feasible.
The property owner, Areim, aimed to prioritize sustainable construction and circular economy principles in the renovation project. This led to an innovative partition wall solution: insulated glass elements from the building’s facade were repurposed as new interior glass partition walls.
“We wanted to make use of materials already present in the building in new ways whenever possible, and began exploring whether reusing window glass for interior partition walls could be a cost-neutral or even profitable solution—one that would save both the environment and expenses.” explains Hanna Koskiahde, Asset Manager at Areim Ab.
Pilot installation confirmed the functionality of glass walls
A prototype partition wall made from window glass was installed in the office building as part of a pilot supported by Helsinki’s Circular Economy Cluster Program, which provided expert assistance and funding for the project.
In the first phase, glass partitions were installed in the building’s lobby, meeting rooms, and a model space on the second floor.
A final comparison conducted at the end of the trial revealed that the costs of partition walls made from reused glass elements were comparable to those of new glass walls, but their carbon footprint was approximately 50% lower. The comparison was carried out by Helsinki-based InLook Oy, the company that manufactured the partition walls.
The lessons from the pilot, which concluded in October 2023, have been compiled into a report intended for use across the real estate and construction industries.
Usability and safety of glass elements in focus
Since the dismantled insulated glass elements were originally designed for facade use, their suitability for indoor applications required careful evaluation.
Usability was studied as early as the project planning phase. While the 20-year-old glass elements no longer met the technical requirements and standards for exterior windows, they were deemed suitable for interior use. Authorities welcomed the trial from the outset, emphasizing the importance of meeting safety standards.
The dismantled glass elements were cleaned and fitted with a certified safety film on both sides to ensure safe use. Their sound insulation properties were assessed in collaboration with an acoustics designer and tested by InLook in its own sound laboratory.
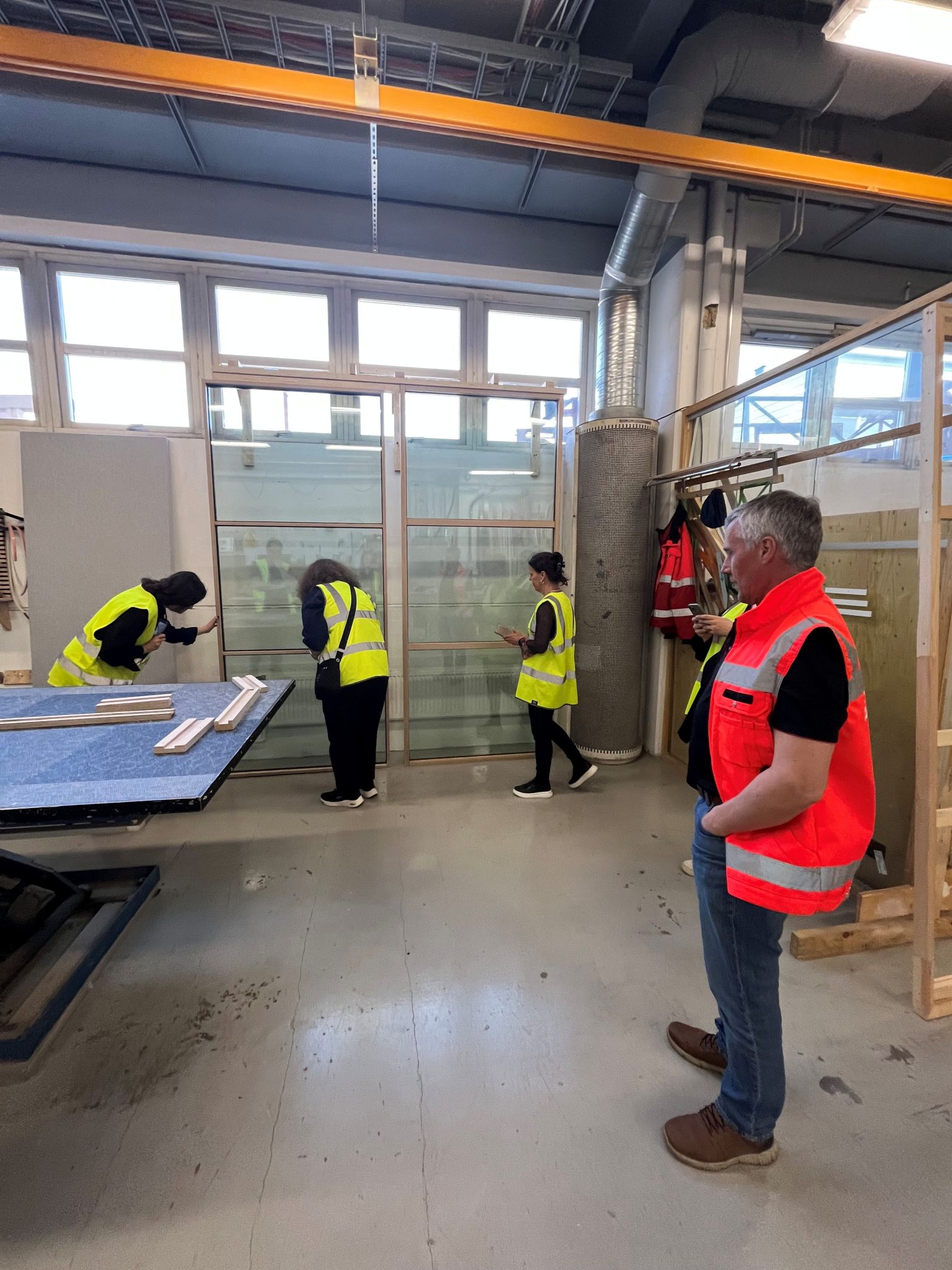
The window elements were installed in birchwood frames designed by Olla Architecture, the project’s lead and architectural designer, and manufactured by InLook. Birch was chosen for its durability and timeless appearance. The partition walls were designed to be long-lasting and movable to accommodate changing spatial needs.
Sustainable construction creates value
The extensive renovation project modernized the building’s outdated technical systems, improved energy efficiency, and adapted the spaces to meet the demands of contemporary office work.
Areim set sustainable construction and environmental friendliness as key objectives from the planning stage, and these principles also guided the selection of circular economy solutions.
The feasibility of circular economy solutions was assessed during project planning through test demolitions and pilot work. In addition to the glass partition walls, many other building structures were given a second life: ceiling slats were refinished and reused, fire doors were refurbished to extend their lifespan, and brass and copper panels removed from the facade were repurposed in the renovated exterior.
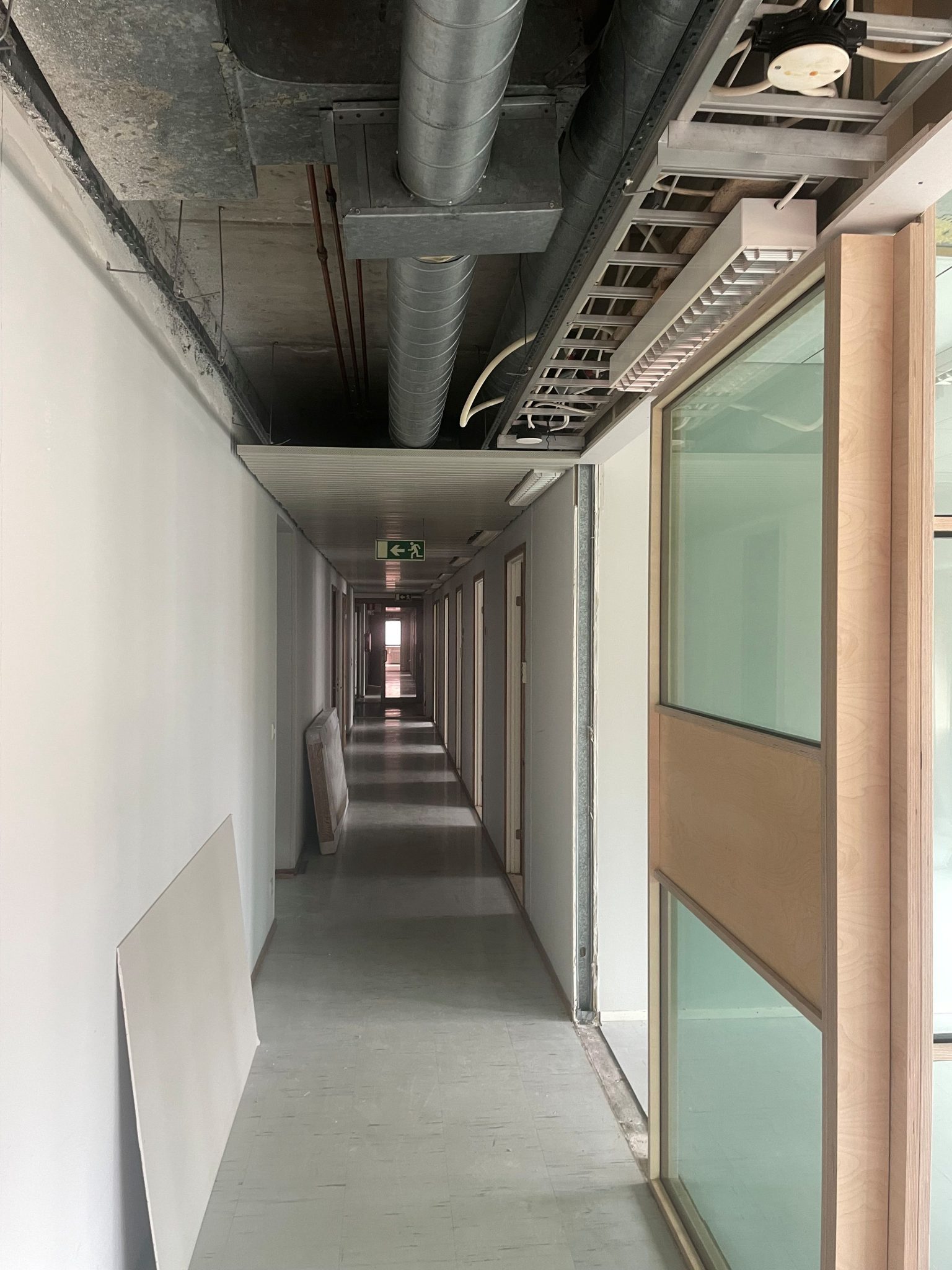
“Making older buildings more environmentally friendly isn’t just an expense—improving energy efficiency also increases their value. The more usable material a building contains, the greater the potential for reuse and the possible cost savings that come with it”, says Hanna Koskiahde.